Nicole Aegerter: Material scientist turned entrepreneur
Material scientist Nicole Aegerter is co-founder of the ETH spin-off Antefil, which produces glass fibre-reinforced plastics for industrial lightweight structures. Nicole talks to us about what motivates her to be part of the circular economy.
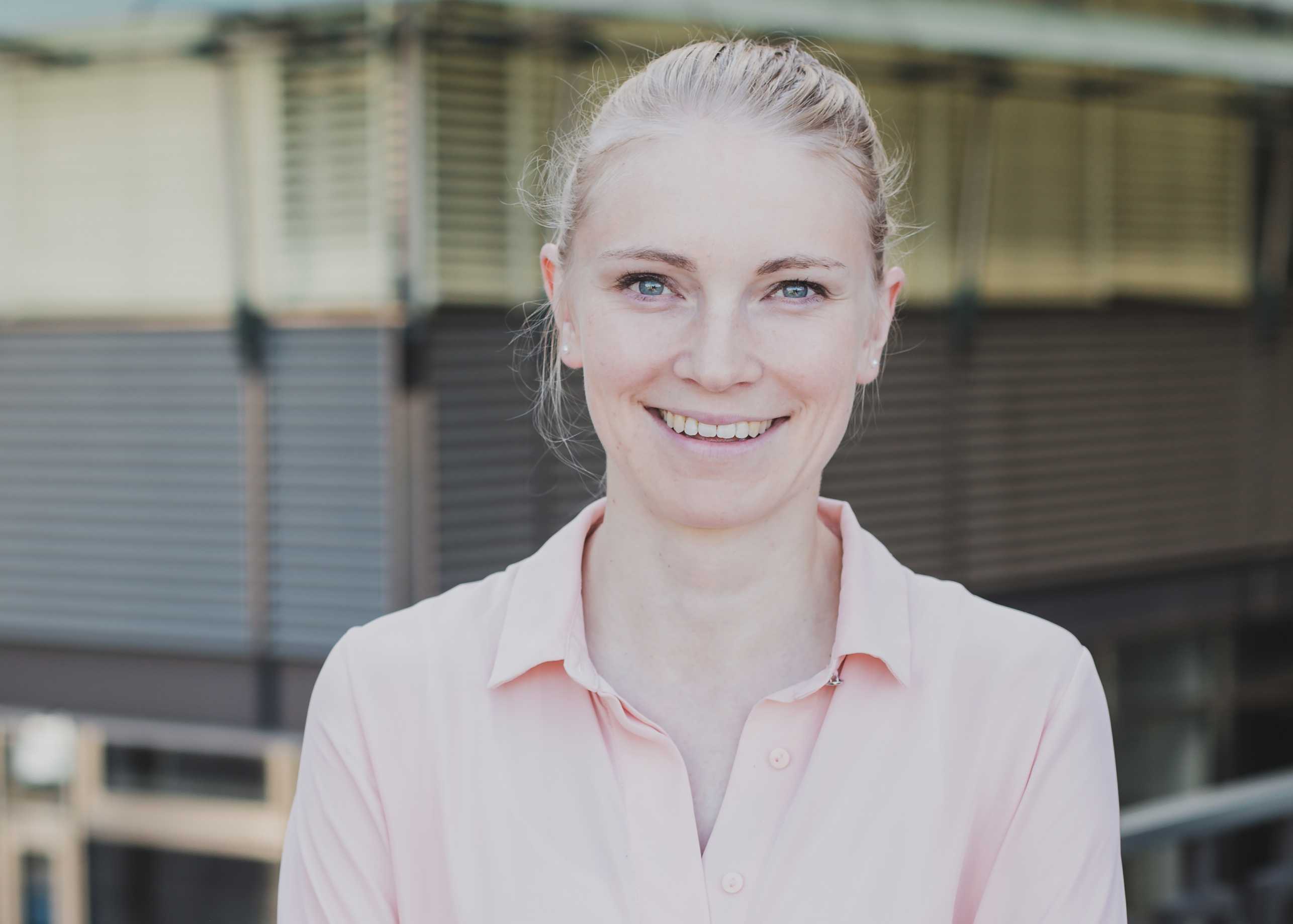
When you were a child, what did you want to be?
Funnily enough I always used to write in friendship books that I wanted to be a researcher. I am not really sure what I thought that would amount to at the time - but that was my dream job.
Why did you study at ETH?
When I was at high school, I really did not get on with economics and languages. But I loved mathematics, physics, biology and chemistry. So I have always been interested in technology and natural sciences.Therefore studying at ETH was the logical next step.
How did you get involved in glass fibre-reinforced plastics and where does your interest in this stem from?
During my Masters, I did my semester and Master’s thesis on the topic and eventually also pursued my doctoral studies in the field. With the developed technology being very industry-relevant, we then decided to commercialise this technology through Antefil Composite Tech.
First and foremost, I was fascinated by combining the benefits of two materials in one new product with enhanced characteristics. Glass fibre-reinforced plastics are used in many different applications, such as sports equipment like tennis rackets or ice hockey sticks or even the blades of wind turbines. You can find these composite materials in all products which are mobile yet also mechanically loaded, and therefore consume less energy if they are light. Today, the processes involved in combining the fibres with plastic are very laborious, which makes them slow and also expensive. And this is the very problem we are working on by combining the processes of fibre production and mixing with plastic.
What motivates you in your work?
For me personally, it is without doubt the fact that we are producing a material, which is consistent with the circular economy. “Sustainability” is a very important issue for me. In our case, this means that we make processes more efficient that produce a lightweight material that consumes less energy during use. Combining these advantages with the possibility for a circular materials economy makes our material more sustainable compared to existing technologies on the market.
How are your plastic fibres different from those produced with standard methods and what benefits do they provide?
The majority of reinforced fibres used today are made from glass because they provide the perfect compromise between material cost, mechanical performance and recyclability at the end of life. Today’s solutions combine the dry fibres with the plastic after fibre production. This process is very slow and often produces poor quality because the material has to flow between the fibres. Air bubbles then also remain in the material, which in turn affects the mechanical strength. And the majority of today’s glass fibre-reinforced plastics cannot even be recycled also due to the use of chemically hardened plastics.
In contrast, we coat every single glass fibre directly with a meltable plastic. The benefit of this approach is that the plastic can be heated later on to form a lightweight structure. This makes the manufacture of components cheaper and more energy efficient, and hence suitable for high-volume applications. The combination of both meltable glass and polymer also means that the component can be fully recycled at the end of its life.
“We want to revolutionise the way in which we produce fibre-reinforced composite materials.”Nicole Aegerter
What are your plans for the future?
We are currently working on a scaled pilot plant so we can increase our material production capacity and run first demonstrator projects with prospective customers. At the moment, we are only able to produce a couple of grams per day but to serve high-volume markets we need to manufacture tons every month. These activities will help us enter our target markets like automotive where lightweight components can reduce the vehicle’s energy consumption. Besides applications with high lot sizes, other applications are large structures, like wind turbine blades, that profit from our material in the reduction of cycle time in manufacturing and recyclability at the end of life.
What career advice would you give to young students already studying technology and natural science or those thinking of such a course?
You never try, you never know! If you never try in the first place and risk that you might fail, you will never know how it might have turned out otherwise.
You have recently started working for Antefil – what was the step from ETH to entrepreneurship like for you?
Exactly, since I finished my PhD I have been working full time for Antefil. But we are still located at ETH. The shift from scientist to entrepreneur is a challenge that I am really enjoying. We are working to make our product marketable, which is in complete contrast to my research at ETH. Nothing is standard and we are trying to create something out of nothing and that is what makes it such good fun.
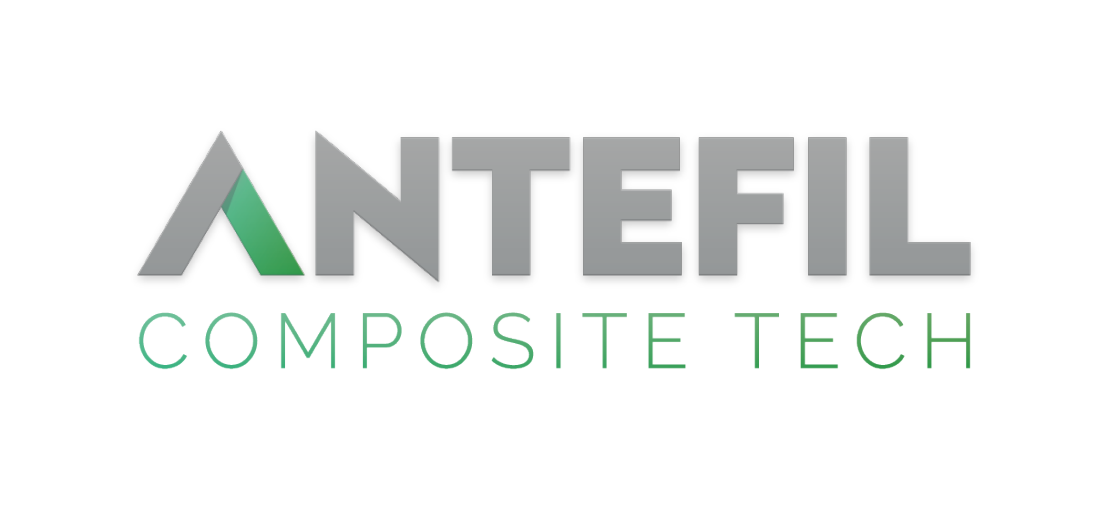
external page Antefil Composite Tech is an ETH spin-off, which emerged from a research project at the Laboratory of Composite Materials and Adaptive Structures at ETH. The company was founded in February 2022.